Plumbing the Depths
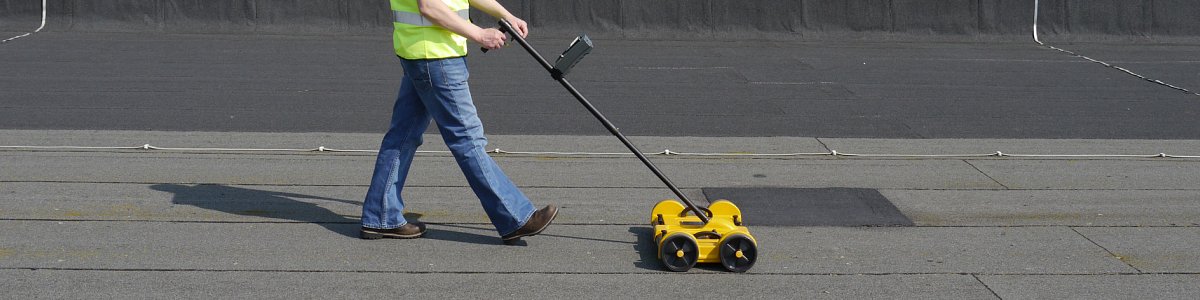
By Paul Franklin, technical manager at RAM Consultancy
When 25mm or 50mm of insulation in a flat roof was the norm, Thermal Performance was still regarded as a luxury by many. Clients often resented the additional cost; “Why can’t I just have a new waterproofing?”; “What use is that to my bottom line?” etc. However, increasing energy prices, fuel shortages, sustainability and demand for higher comfort levels now require more insulation. Successive revisions of the Building Regulations have raised the bar substantially, with 130mm of efficient insulation now being standard in flat roofs. Emphasis on building performance has never been stronger, with monitoring becoming a real factor, plus the financial climate is causing distress. Minimising cost is now essential to survival. Readers associated with flat roofing will be aware of the importance of keeping water out of the building and of ensuring the build-up is kept dry. Any water trapped in the build-up will develop into leaks and degrade the thermal performance. Trapped water can derive from a number of sources:
- Water can be trapped during construction: rain on the underlay or between the insulation boards of a part-finished roof, if not removed can become trapped beneath the final layers.
- If the insulation is not kept protected and dry on-site, it can absorb water and transfer this into the roof when laid.
- If the moisture potentials and vapour control are not designed adequately or components are poorly installed, water vapour can permeate through from below and condense within the insulation.
- Leaks will wet the insulation and water may gather in the roof before it appears inside. There is a need for a relatively simple and costeffective method of identifying and mapping how far water has spread in a roof area, so that the roof can be reliably repaired, either by stripping out all damaged insulation followed by localised or complete overlaying, or by Vacuum Dewatering to refresh the insulation and repairs as required.
Electrical Capacitance Testing (ECT)
The Electrical Capacitance Meter is used to assess the presence and spread of moisture in a roof. The most widely-known unit is called the ‘DecScanner’, which has been in use in the UK and North America for around thirty years. This wheeled 10kg trolley device is the width of a roll of RBM roofing membrane and is pushed around the roof in a pattern similar to using a lawn mower.
The origional DecScanner, in use since the 1980s. The new DecScanner will provide results up to 150mm below the roof surface.
How does it work?
We all know that wet clothes are poor insulators compared to dry ones. When insulation becomes damp or wet, its thermal efficiency changes but so do the electrical properties. The Capacitance Meter change can sense this from above a roofing
membrane without puncturing it.
The equipment transmits low frequency signals from pads on the underside through the membrane and into the insulation (or other substrate) and the ‘echoes’ are received by the machine. The response reveals the impedance of the substrate and the wetter it is the greater the impedance.
The meter and a buzzer alert the operator to elevated levels of moisture. By steering around a reading area, the pocket of stronger readingsindicating entrapped moisture can be mapped and marked onto the roof surface.
The DecScanner can be used in two ways:
- Where the construction is unsuitable for conventional (‘Wet’ or ‘Dry’) electronic leak detection, an inspector can locate pockets of water likely to be below a leak, thus focussing his attention and scrutiny on a small area to find the defect.
- To differentiate areas with trapped moisture from dry areas, so that a detailed map and stripping or de-watering can be used on only those areas, rather than a full and costly reroofing project.
It should be noted that the principle of Capacitance Testing requires the roof surface to be completely dry – the scanner cannot be expected to seek out small pockets of water beneath the roof membranes through a layer of surface water!
Calibration
As with any sophisticated item of equipment, the ECT scanner will require proper calibration to provide the most reliable results. Setting a zero point over the driest / highest point on the roof will provide relative moisture levels, which is usually adequate for use 1) above. For Moisture Mapping (use 2), a full calibration to confirm absolute (actual) moisture levels is always recommended and is achieved as follows:
- Briefly walk the roof with the DecScanner to find the spot with the lowest possible reading. This is likely to be in an area with no reported leaks, and usually towards the upper end of any roof falls, away from gutter areas.
- A careful core sample at this point will serve two purposes. It will confirm the full roof buildup (which often varies from the reported components!) and also, the actual condition of the substrate can be determined; is the insulation / screed actually Dry or Damp or possibly even Wet to the touch? If it is indeed Dry, then this forms a reliable Zero point to set the meter. The core must be properly re-sealed, of course.
- Another brief scan over the roof to locate the highest reading area; this could be anywhere between 50% and 100% and may even cause the needle to bounce off the upper stop.
- Take a second core sample and check the substrate – is it Very Damp or Wet or completely saturated / awash with trapped water. If Wet or worse, then this is a valid 100% point and the meter should be set now to 100%.
- Scan the roof for an area reading around 60% and take your third core sample. The moisture / water within the substrate should ideally be at a threshold level between Very Damp (not sufficient ‘free’ water to warrant stripping) and Wet (where it is possible / viable to extract water from the layer by Vacuum De-Watering to improve its condition).
-
This threshold is the key to Mapping; all areas reading higher will either require stripping and replacement before any overlaying work commences, or they can receive DWV (De- Watering by Vacuum) to refresh the insulation or screed prior to the overlaying.
-
If the third core is inconclusive, then a fourth will be required to find a suitable threshold level for mapping the roof.
Mapping procedure
Once calibrated, the DecScanner should be walked over the entire area in a systematic manner, not unlike mowing a lawn to produce striping. Areas with readings elevated above the threshold are marked directly onto the roof surface with wax crayon, (and onto a roof plan for reference), to produce a contour map showing where the water levels are of concern; see typical plan below:
The pros and cons
Capacitance testing has several advantages:
- The method works well on smooth or mineral RBMs or over chippings, plus most single-ply membranes (PVC, EVA, VET, TPO, TPE), as long as the surface is dry.
- Identifies entrapped water beneath the membrane without stripping.
- Large areas of roofing can be scanned and mapped relatively quickly, especially on large open roof areas, giving a swift overall picture and assessment of the roof condition.
- As long as the surface is dry, mapping can proceed in hot, cold or windy conditions.
- Unlike a thermographic survey, a thermal gradient through the roof is not required, so it can be used on an unheated building.
- The membrane only requires cutting at the specific core sample sites for calibration.
Limitations in use:
- Conductive surfaces (a film of water, a highcarbon black EPDM, a foil-surfaced bitumen membrane or a foil-faced insulation board) will create false high readings and invalid results.
- Without coring, absolute moisture or water quantities will not be available.
- It will not pinpoint a leak pathway, merely focus attention and scrutiny on the wetted area.
- The equipment has a limited depth of sensing, or range.
The original DecScanner can sense down approximately 100mm below the upper surface, adequate for insulation up to 90mm thick, i.e. roofs installed up to 2010. Since the 2010 Building Regulations, 120/130mm thick PU insulation is required to meet flat roof ‘U-Values’, well outside the range of the original model. After extensive development, an improved model (left), effective down to 150mm has been introduced, enabling current projects to be successfully scanned and mapped. As part of RAM Consultancy’s commitment to servicing every client requirement, we have invested in this latest DecScanner.
Summary
Capacitance Testing is very useful, assisting leak tracing where ELD testing will not work and in identifying the extent of wet insulation in a roof, which is critical when considering refurbishment. If used to enable only partial stripping (or De- Watering) instead of a full strip-up, the major savings in waste disposal, new materials, labour and time lead to substantial monetary and environmental benefits for all parties and for the planet.
RAM Consultancy is a dedicated building envelope consultant and leak detection organisation. Visit: www.roofconsultancy.com or to discuss your requirements with a member of the team tel: 0844 335 1822